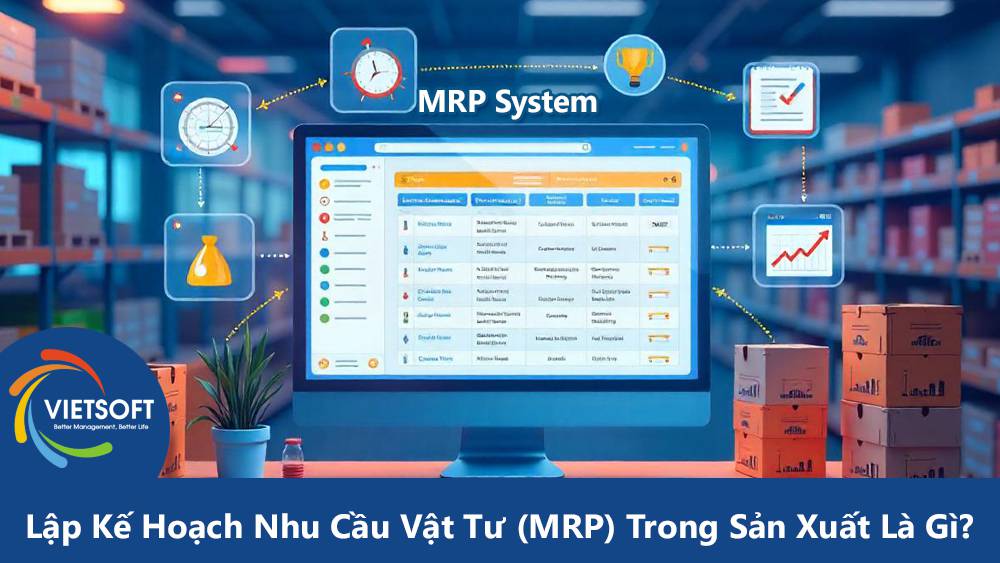
Trong lĩnh vực sản xuất, việc quản lý nguyên vật liệu một cách hiệu quả là yếu tố sống còn để đảm bảo quy trình vận hành trơn tru, đáp ứng nhu cầu khách hàng và tối ưu hóa chi phí. Một trong những công cụ quan trọng hỗ trợ doanh nghiệp đạt được mục tiêu này chính là Lập kế hoạch nhu cầu vật tư (Material Requirements Planning – MRP). Bài viết sau sẽ giải thích chi tiết về khái niệm này, vai trò của nó trong sản xuất, cách thức hoạt động cũng như những lợi ích mà nó mang lại.
I. Lập Kế Hoạch Nhu Cầu Vật Tư (MRP) Là Gì?
Lập kế hoạch nhu cầu vật tư (MRP) là một hệ thống quản lý sản xuất được thiết kế để tính toán và lập kế hoạch cho nhu cầu nguyên vật liệu cần thiết nhằm đáp ứng kế hoạch sản xuất và đơn hàng của khách hàng. Đây là một công cụ hoặc phần mềm giúp doanh nghiệp xác định:
- Cần những nguyên vật liệu nào?
- Số lượng bao nhiêu?
- Khi nào cần chúng?
Ra đời từ những năm 1960 tại Mỹ, MRP nhanh chóng trở thành một “ứng dụng đột phá” trong ngành sản xuất, mở đường cho việc áp dụng rộng rãi phần mềm kinh doanh và máy tính vào quản lý sản xuất. Ngày nay, MRP đã phát triển vượt bậc, tích hợp với các hệ thống hiện đại để hỗ trợ doanh nghiệp trong môi trường cạnh tranh khốc liệt.
Tại Việt Nam, với sự phát triển mạnh mẽ của ngành sản xuất như dệt may, điện tử, và cơ khí, MRP đóng vai trò quan trọng trong việc giúp các doanh nghiệp tối ưu hóa nguồn lực, giảm lãng phí và nâng cao khả năng cạnh tranh.
II. Vai Trò Của Lập Kế Hoạch Nhu Cầu Vật Tư Trong Sản Xuất
MRP không chỉ là một công cụ tính toán mà còn là “trái tim” của hệ thống quản lý sản xuất hiện đại. Dưới đây là những vai trò nổi bật của MRP mà bất kỳ nhà quản lý sản xuất nào cũng cần nắm rõ:
1. Đảm Bảo Nguyên Vật Liệu Sẵn Sàng Đúng Thời Điểm
MRP giúp doanh nghiệp dự đoán chính xác thời điểm cần nguyên vật liệu để sản xuất, từ đó tránh tình trạng thiếu hụt hoặc gián đoạn dây chuyền sản xuất. Ví dụ, một nhà máy sản xuất linh kiện điện tử tại Việt Nam có thể sử dụng MRP để đảm bảo chip bán dẫn được nhập đúng ngày trước khi bắt đầu lắp ráp.
2. Tối Ưu Hóa Hàng Tồn Kho
Hàng tồn kho quá nhiều đồng nghĩa với việc vốn bị “đóng băng”, trong khi quá ít lại gây rủi ro ngừng sản xuất. MRP giúp duy trì mức tồn kho tối ưu, giảm chi phí lưu kho và hạn chế lãng phí nguyên vật liệu hết hạn hoặc lỗi thời.
3. Cải Thiện Hiệu Suất Sản Xuất
Bằng cách lập lịch trình sản xuất dựa trên nhu cầu thực tế, MRP đảm bảo các giai đoạn sản xuất được phối hợp nhịp nhàng, tránh tình trạng “chờ đợi” hoặc “quá tải” tại một công đoạn nào đó.
4. Đáp Ứng Nhu Cầu Khách Hàng Nhanh Chóng
Trong bối cảnh thị trường Việt Nam ngày càng yêu cầu giao hàng nhanh, MRP hỗ trợ doanh nghiệp đáp ứng đơn hàng đúng hạn, nâng cao sự hài lòng của khách hàng và giữ vững uy tín thương hiệu.
5. Giảm Chi Phí Và Tăng Cường Quản Lý Chuỗi Cung Ứng
MRP không chỉ tối ưu nội bộ mà còn hỗ trợ quản lý mối quan hệ với nhà cung cấp, giúp lên kế hoạch đặt hàng chính xác, giảm chi phí mua sắm không cần thiết.
III. Hệ Thống MRP Hoạt Động Như Thế Nào?
Để hiểu rõ cách MRP vận hành, chúng ta cần nhìn vào quy trình cơ bản của nó. Dưới đây là các bước hoạt động chính của một hệ thống MRP được giải thích một cách dễ hiểu:
Bước 1 – Xác Định Nhu Cầu Sản Xuất
Hệ thống bắt đầu bằng việc phân tích đơn hàng từ khách hàng hoặc dự báo nhu cầu sản phẩm trong tương lai. Ví dụ, nếu một công ty sản xuất giày dép nhận đơn hàng 10.000 đôi giày trong tháng tới, MRP sẽ tính toán lượng da, đế giày và chỉ may cần thiết.
Bước 2 – Kiểm Tra Danh Mục Nguyên Vật Liệu (BOM)
Danh mục nguyên vật liệu (Bill of Materials – BOM) là “bản đồ” chi tiết liệt kê tất cả các thành phần cần thiết để sản xuất một sản phẩm. MRP sử dụng BOM để xác định từng loại vật tư và số lượng tương ứng.
Bước 3 – Đánh Giá Tồn Kho Hiện Có
MRP kiểm tra lượng nguyên vật liệu hiện có trong kho để tính toán nhu cầu bổ sung. Ví dụ, nếu kho đã có 500 mét vải nhưng cần 1.000 mét để sản xuất, hệ thống sẽ yêu cầu nhập thêm 500 mét.
Bước 4 – Lập Kế Hoạch Mua Sắm Và Sản Xuất
Dựa trên thời gian chờ (lead time) từ nhà cung cấp và lịch trình sản xuất, MRP đưa ra kế hoạch chi tiết về thời điểm đặt hàng hoặc sản xuất các linh kiện, nguyên vật liệu.
Bước 5 – Theo Dõi Và Điều Chỉnh Liên Tục
MRP không phải là hệ thống “cài đặt và quên”. Nó liên tục cập nhật dữ liệu thực tế (như thay đổi đơn hàng hoặc chậm trễ giao hàng) để điều chỉnh kế hoạch, đảm bảo mọi thứ luôn “đúng nhịp”.
IV. So Sánh các hệ thống MRP, MES Và ERP – Sự Khác Biệt Là Gì?
Trong quản lý sản xuất, ba hệ thống phổ biến là MRP (Material Requirements Planning), MES (Manufacturing Execution System) và ERP (Enterprise Resource Planning) thường được nhắc đến. Nhưng chúng khác nhau như thế nào? Hãy cùng phân tích từng hệ thống để hiểu rõ vai trò và ứng dụng của chúng trong doanh nghiệp.
1. Hệ thống MRP – Lập Kế Hoạch Nhu Cầu Vật Tư
MRP là hệ thống chuyên biệt tập trung vào lập kế hoạch nhu cầu vật tư và quản lý nguyên vật liệu cho sản xuất. Mục tiêu chính của MRP là đảm bảo doanh nghiệp có đủ nguyên vật liệu cần thiết, đúng số lượng và đúng thời điểm để đáp ứng kế hoạch sản xuất. Nó hoạt động dựa trên dữ liệu như danh mục nguyên vật liệu (BOM), tồn kho hiện có và dự báo nhu cầu.
- Điểm mạnh: Tối ưu hóa quản lý nguyên vật liệu, giảm tồn kho dư thừa, hỗ trợ lập lịch sản xuất.
- Ứng dụng: Phù hợp cho các doanh nghiệp tập trung vào dây chuyền sản xuất, như nhà máy sản xuất linh kiện ô tô tại Hải Phòng chỉ cần quản lý nguyên liệu thép và nhựa.
- Hạn chế: Chỉ giới hạn ở khâu lập kế hoạch vật tư, không bao quát các hoạt động khác ngoài sản xuất.
2. Hệ thống MES – Hệ Thống Điều Hành Sản Xuất
MES là hệ thống giám sát và điều hành sản xuất theo thời gian thực, tập trung vào việc quản lý và thực thi các hoạt động trên sàn nhà máy. Nó theo dõi tiến độ sản xuất, hiệu suất máy móc, chất lượng sản phẩm và lao động ngay tại dây chuyền.
- Điểm mạnh: Cung cấp dữ liệu thời gian thực, cải thiện hiệu suất sản xuất, giảm sai sót trong quá trình vận hành.
- Ứng dụng: Thích hợp cho các nhà máy cần kiểm soát chặt chẽ hoạt động sản xuất, chẳng hạn như một xưởng dệt may tại Đồng Nai muốn theo dõi sản lượng vải từng giờ.
- Hạn chế: Không tập trung vào lập kế hoạch dài hạn hay quản lý tài nguyên ngoài sàn sản xuất.
3. Hệ thống ERP – Kế Hoạch Nguồn Lực Doanh Nghiệp
ERP là hệ thống toàn diện, tích hợp tất cả các hoạt động kinh doanh từ sản xuất, tài chính, nhân sự, đến marketing và chuỗi cung ứng. MRP và MES có thể được xem như các module trong ERP, nhưng ERP vượt xa hơn với khả năng quản lý tổng thể doanh nghiệp.
- Điểm mạnh: Tích hợp toàn bộ quy trình kinh doanh, hỗ trợ ra quyết định chiến lược, tối ưu hóa nguồn lực toàn diện.
- Ứng dụng: Phù hợp cho các doanh nghiệp lớn tại Việt Nam muốn quản lý đồng bộ mọi khía cạnh, ví dụ một tập đoàn sản xuất đồ gia dụng cần theo dõi từ nguyên vật liệu, sản xuất đến phân phối.
- Hạn chế: Chi phí triển khai cao, đòi hỏi thời gian và nguồn lực để tích hợp.
V. Lợi Ích Của Hệ Thống MRP Trong Sản Xuất
Sử dụng MRP mang lại nhiều lợi ích thiết thực cho doanh nghiệp, đặc biệt trong bối cảnh sản xuất hiện đại tại Việt Nam:
1. Tăng Cường Khả Năng Dự Báo
MRP cung cấp dữ liệu chính xác để dự báo nhu cầu nguyên vật liệu, giúp doanh nghiệp chuẩn bị tốt hơn trước những biến động thị trường.
2. Giảm Thiểu Lãng Phí
Bằng cách chỉ mua hoặc sản xuất đúng số lượng cần thiết, MRP giúp giảm lượng nguyên vật liệu dư thừa hoặc hết hạn sử dụng.
3. Nâng Cao Hiệu Quả Quản Lý
Tự động hóa quy trình lập kế hoạch giúp giảm thiểu sai sót do con người, đồng thời tiết kiệm thời gian cho các nhà quản lý.
4. Ứng Phó Với Rủi Ro Chuỗi Cung Ứng
Trong trường hợp xảy ra gián đoạn (như thiên tai hoặc thiếu hụt nguyên liệu), MRP hỗ trợ điều chỉnh kế hoạch nhanh chóng để duy trì sản xuất.
VI. Thách Thức Khi Áp Dụng Lập Kế Hoạch Nhu Cầu Vật Tư
Dù có nhiều lợi ích, MRP cũng đối mặt với một số thách thức mà doanh nghiệp Việt Nam cần lưu ý:
- Dữ Liệu Đầu Vào Không Chính Xác: Nếu thông tin về tồn kho, đơn hàng hoặc BOM không đúng, kết quả từ MRP sẽ sai lệch.
- Phụ Thuộc Vào Công Nghệ: Doanh nghiệp cần đầu tư vào phần mềm và đào tạo nhân viên để sử dụng hiệu quả.
- Biến Động Thị Trường: Dự báo sai nhu cầu có thể dẫn đến tồn kho dư thừa hoặc thiếu hụt nguyên vật liệu.
Để khắc phục, doanh nghiệp nên kết hợp MRP với các phương pháp khác như JIT (Just-in-Time) hoặc Kanban để tăng tính linh hoạt.
VII. MES SmartTrack – Giải Pháp Tăng Cường Hiệu Quả Lập Kế Hoạch Nhu Cầu Vật Tư
Tại Việt Nam, việc triển khai hệ thống giám sát sản xuất như MES SmartTrack của công ty Vietsoft đang trở thành xu hướng giúp doanh nghiệp tối ưu hóa MRP. MES SmartTrack không chỉ theo dõi tiến độ sản xuất theo thời gian thực mà còn tích hợp với MRP để:
- Cung cấp dữ liệu chính xác về tồn kho và tiến độ sản xuất.
- Tự động điều chỉnh kế hoạch khi có sự thay đổi từ đơn hàng hoặc nhà cung cấp.
- Giảm thiểu sai sót trong quản lý nguyên vật liệu.
Bạn muốn khám phá cách MES SmartTrack nâng tầm hiệu quả sản xuất? Xin vui lòng tham khảo giải pháp Hệ thống giám sát sản xuất MES SmartTrack tại đây
Hoặc liên hệ để nhận tư vấn theo hotline: 0986778578 hoặc email sales@vietsoft.com.vn
VII. Kết Luận
Lập kế hoạch nhu cầu vật tư (MRP) là một công cụ không thể thiếu trong quản lý sản xuất hiện đại, đặc biệt tại thị trường Việt Nam đang phát triển mạnh mẽ. Từ việc đảm bảo nguyên vật liệu sẵn sàng, tối ưu hóa tồn kho đến nâng cao hiệu suất sản xuất, MRP giúp doanh nghiệp đứng vững trong môi trường cạnh tranh khốc liệt. Khi kết hợp với các giải pháp công nghệ như MES SmartTrack, MRP càng trở nên mạnh mẽ, mang lại lợi thế vượt trội cho doanh nghiệp.
Hãy bắt đầu áp dụng MRP ngay hôm nay để tối ưu hóa quy trình sản xuất của bạn! Nếu bạn cần thêm thông tin hoặc tư vấn, đừng ngần ngại liên hệ với các chuyên gia tại Vietsoft để nhận giải pháp phù hợp nhất.