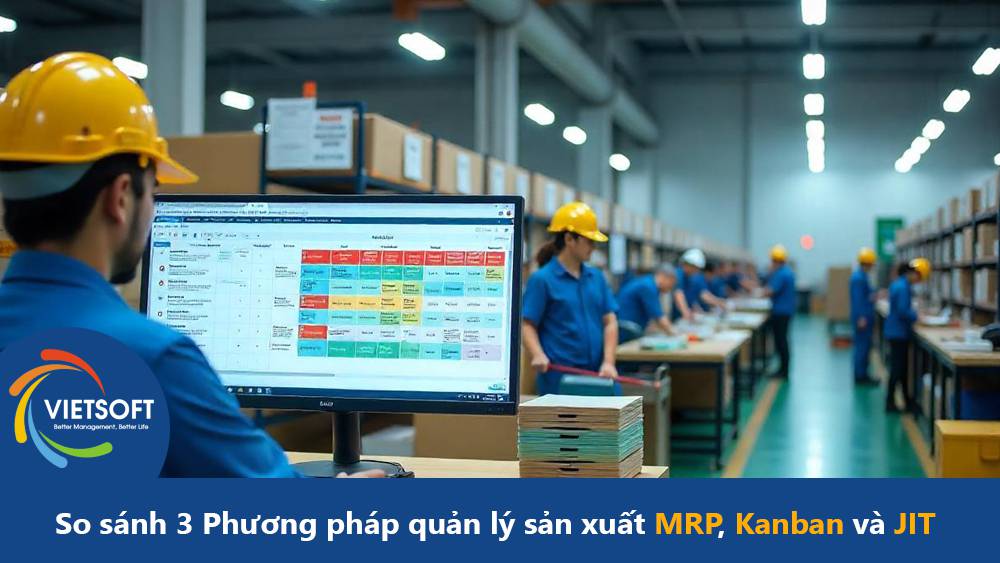
Trong bối cảnh cạnh tranh ngày càng khốc liệt của ngành sản xuất tại Việt Nam, việc tăng thông lượng throughput không chỉ là một mục tiêu mà còn là chìa khóa để doanh nghiệp tối ưu hóa hiệu suất, giảm chi phí và gia tăng lợi nhuận. Bài viết sau sẽ chia sẻ những chiến lược thực tiễn, kiến thức chuyên sâu và các phương pháp tiên tiến để bạn có thể nâng cao thông lượng một cách bền vững. Hãy cùng tìm hiểu nhé!
I. Tăng Thông Lượng Throughput Là Gì Và Tại Sao Quan Trọng?
Thông lượng (Throughput) là thước đo tốc độ mà một hệ thống sản xuất tạo ra sản phẩm hoàn thiện trong một khoảng thời gian nhất định. Vậy tăng thông lượng throughput nghĩa là làm thế nào để sản xuất được nhiều sản phẩm hơn trong cùng một khoảng thời gian hoặc giảm thời gian cần thiết để hoàn thành cùng một lượng sản phẩm.
Tại sao điều này quan trọng? Trong sản xuất, thông lượng cao đồng nghĩa với việc bạn có thể đáp ứng nhu cầu thị trường nhanh chóng, giảm tồn kho, tối ưu hóa tài nguyên và cải thiện lợi tức đầu tư (ROI). Từ kinh nghiệm thực tế, tôi nhận thấy rằng các doanh nghiệp tập trung vào tăng thông lượng thường đạt được lợi thế cạnh tranh vượt trội, đặc biệt trong các ngành công nghiệp đòi hỏi tốc độ như may mặc, điện tử hay thực phẩm.
II. Những Thách Thức Khi Tăng Thông Lượng Throughput
Trước khi đi vào các giải pháp, chúng ta cần hiểu rõ những “rào cản” phổ biến mà tôi đã gặp trong suốt sự nghiệp khi hỗ trợ các nhà máy tối ưu hóa thông lượng:
1. Điểm Nghẽn Tàng Ẩn Trong Quy Trình
Điểm nghẽn (bottlenecks) không phải lúc nào cũng dễ phát hiện. Ví dụ, một công đoạn tưởng chừng nhỏ như kiểm tra chất lượng có thể làm chậm toàn bộ dây chuyền nếu không được tối ưu.
2. Thiếu Dữ Liệu Thời Gian Thực
Nhiều nhà máy vẫn dựa vào báo cáo thủ công, dẫn đến việc không thể phản ứng kịp thời khi thông lượng giảm đột ngột.
3. Quá Tải Tài Nguyên
Khi cố gắng tăng thông lượng bằng cách đẩy nhanh tốc độ, máy móc và nhân viên có thể bị quá tải, gây ra hỏng hóc hoặc sai sót.
III. Các Chiến Lược Tiên Tiến Để Tăng Thông Lượng Throughput
Dựa trên kinh nghiệm thực chiến và những tiến bộ công nghệ mới nhất, tôi xin chia sẻ các chiến lược hiệu quả để tăng thông lượng throughput trong sản xuất:
1. Áp Dụng Phương Pháp Lean Và Kaizen
Lean (sản xuất tinh gọn) và Kaizen (cải tiến liên tục) là hai triết lý mà tôi đã áp dụng thành công tại nhiều nhà máy. Lean giúp loại bỏ lãng phí như thời gian chờ, tồn kho dư thừa hay các công đoạn không tạo giá trị. Trong khi đó, Kaizen khuyến khích nhân viên đóng góp ý tưởng cải tiến nhỏ nhưng liên tục. Ví dụ, một nhà máy lắp ráp điện tử tại Việt Nam đã tăng thông lượng lên 25% chỉ bằng cách sắp xếp lại vị trí công cụ để giảm thời gian di chuyển của công nhân.
2. Tối Ưu Hóa Điểm Nghẽn Với Lý Thuyết Ràng Buộc (TOC)
Theo Theory of Constraints (TOC), để tăng thông lượng throughput, bạn cần tập trung vào “mắt xích yếu nhất”. Hãy xác định điểm nghẽn chính (có thể là một máy móc chậm hoặc một công đoạn phức tạp), sau đó tối ưu hóa nó bằng cách tăng công suất, giảm thời gian xử lý hoặc phân bổ thêm tài nguyên. Tôi từng hỗ trợ một nhà máy giấy tăng thông lượng từ 50 tấn/ngày lên 70 tấn/ngày chỉ bằng cách điều chỉnh tốc độ máy cắt – điểm nghẽn lớn nhất của họ.
3. Sử Dụng Phân Tích Dữ Liệu Lớn (Big Data)
Trong kỷ nguyên 4.0, dữ liệu là “vàng”. Phân tích dữ liệu lớn từ các cảm biến IoT trên dây chuyền sản xuất có thể dự đoán xu hướng thông lượng và phát hiện bất thường trước khi chúng xảy ra. Chẳng hạn, nếu dữ liệu cho thấy một máy dệt có xu hướng giảm tốc độ sau 100 giờ hoạt động, bạn có thể lên lịch bảo trì trước, tránh gián đoạn sản xuất.
4. Tự Động Hóa Các Công Đoạn Lặp Lại
Tự động hóa không chỉ tăng tốc độ mà còn giảm sai sót. Ví dụ, thay vì để công nhân kiểm tra thủ công từng sản phẩm, bạn có thể sử dụng máy quét tự động để kiểm tra chất lượng, vừa nhanh vừa chính xác. Một nhà máy thực phẩm mà tôi từng tư vấn đã tăng thông lượng lên 40% nhờ tích hợp robot đóng gói.
IV. Công Thức Đo Lường Và Đánh Giá Hiệu Quả Tăng Thông Lượng
Để biết liệu các nỗ lực tăng thông lượng throughput của bạn có thành công hay không, bạn cần đo lường chính xác. Công thức cơ bản vẫn là:
Thông lượng (T) = Tổng số sản phẩm hoàn thiện (I) / Tổng thời gian sản xuất (F)
- I: Số lượng sản phẩm được sản xuất trong một khoảng thời gian.
- F: Thời gian từ khi bắt đầu đến khi kết thúc quá trình sản xuất.
Ví dụ thực tế: Một nhà máy sản xuất giày hoàn thành 500 đôi giày trong 10 giờ. Thông lượng ban đầu là 50 đôi/giờ. Sau khi tối ưu hóa bằng cách giảm thời gian chờ giữa các công đoạn, họ hoàn thành 500 đôi trong 8 giờ, tăng thông lượng lên 62,5 đôi/giờ – cải thiện 25%.
Ngoài ra, bạn cũng nên theo dõi Tỷ lệ thông lượng tối đa (Throughput Yield), được tính bằng cách nhân tỷ lệ sản phẩm đạt chất lượng ở mỗi công đoạn. Nếu mỗi công đoạn có tỷ lệ lỗi 5%, thông lượng tối đa sẽ giảm đáng kể qua nhiều bước.
V. Vai Trò Của Công Nghệ Trong Việc Tăng Thông Lượng Throughput
Công nghệ hiện đại đóng vai trò then chốt trong việc nâng cao thông lượng. Dưới đây là những ứng dụng mà tôi đánh giá cao từ kinh nghiệm thực tế:
1. Hệ Thống MES (Manufacturing Execution System)
MES cung cấp khả năng giám sát toàn diện, từ quản lý đơn hàng, theo dõi tiến độ đến phân tích hiệu suất máy móc. Một hệ thống MES tốt có thể giảm tới 30% thời gian ngừng hoạt động không kế hoạch, từ đó tăng thông lượng đáng kể.
2. AI Và Machine Learning
Trí tuệ nhân tạo (AI) có thể dự đoán thời điểm máy móc cần bảo trì hoặc đề xuất cách sắp xếp lịch sản xuất tối ưu. Tôi từng chứng kiến một nhà máy ô tô sử dụng AI để giảm 15% thời gian chuyển đổi sản phẩm giữa các dòng xe, giúp tăng thông lượng lên 18%.
3. IoT Và Cảm Biến Thông Minh
Cảm biến IoT thu thập dữ liệu từ từng máy móc, giúp bạn biết chính xác tốc độ sản xuất, thời gian ngừng máy và các yếu tố khác ảnh hưởng đến thông lượng. Điều này đặc biệt hữu ích trong các ngành sản xuất liên tục như hóa chất hay thép.
VI. MES SmartTrack – Giải Pháp Tăng Thông Lượng Tại Việt Nam
Nói đến công nghệ hỗ trợ tăng thông lượng throughput, tôi không thể không nhắc đến MES SmartTrack – giải pháp giám sát sản xuất do Vietsoft phát triển. Với khả năng tích hợp IoT, phân tích dữ liệu thời gian thực và giao diện thân thiện, MES SmartTrack đã giúp hàng loạt doanh nghiệp Việt Nam cải thiện thông lượng một cách ấn tượng.
Ví dụ, một nhà máy dệt may tại Đồng Nai sử dụng MES SmartTrack để theo dõi hiệu suất từng máy dệt. Nhờ phát hiện sớm các máy có tốc độ chậm, họ đã tăng thông lượng từ 100 cuộn vải/ngày lên 130 cuộn/ngày chỉ trong 2 tháng. Điều đặc biệt là giải pháp này được thiết kế phù hợp với đặc thù sản xuất tại Việt Nam, từ chi phí hợp lý đến khả năng tùy chỉnh cao.
Bạn tò mò MES SmartTrack có thể giúp nhà máy của bạn như thế nào?
Xin vui lòng tham khảo giải pháp Hệ thống giám sát sản xuất MES SmartTrack tại đây
Hoặc liên hệ để nhận tư vấn theo hotline: 0986778578 hoặc email sales@vietsoft.com.vn
VII. Lợi Ích Thực Tiễn Khi Tăng Thông Lượng Throughput
Khi bạn thành công trong việc tăng thông lượng throughput, những lợi ích sau sẽ xuất hiện:
1. Tăng Năng Suất: Sản xuất nhiều hơn trong thời gian ngắn hơn, đáp ứng nhu cầu thị trường nhanh chóng.
2. Giảm Chi Phí Vận Hành: Tối ưu hóa tài nguyên giúp tiết kiệm nguyên liệu, năng lượng và nhân công.
3. Cải Thiện Chất Lượng Dịch Vụ: Giao hàng đúng hạn, tăng sự hài lòng của khách hàng.
4. Tăng Khả Năng Cạnh Tranh: Doanh nghiệp của bạn sẽ nổi bật hơn so với đối thủ nhờ hiệu suất vượt trội.
VIII. Kết Luận
Tăng thông lượng throughput không chỉ là một kỹ thuật mà là cả một nghệ thuật trong quản lý sản xuất. Từ việc áp dụng Lean, TOC, đến tích hợp công nghệ hiện đại như MES SmartTrack, tất cả đều hướng đến mục tiêu giúp doanh nghiệp của bạn hoạt động hiệu quả hơn, cạnh tranh mạnh mẽ hơn. Hãy bắt đầu bằng cách đánh giá thông lượng hiện tại của bạn và thử nghiệm một trong những chiến lược mà tôi đã chia sẻ.
Nếu bạn cần một giải pháp toàn diện để nâng cao thông lượng, đừng bỏ lỡ MES SmartTrack từ Vietsoft – công cụ đã được kiểm chứng bởi hàng trăm nhà máy tại Việt Nam. Chúc bạn thành công trong hành trình tối ưu hóa sản xuất!
Phương pháp quản lý sản xuất là nền tảng giúp doanh nghiệp tối ưu hóa quy trình, giảm chi phí và đáp ứng nhu cầu khách hàng. Trong bài viết này, chúng ta sẽ so sánh ba phương pháp phổ biến: Material Requirements Planning (MRP), Kanban và Just In Time (JIT). Mỗi phương pháp có cách tiếp cận khác nhau, từ lập kế hoạch chi tiết (MRP) đến quản lý dòng chảy linh hoạt (Kanban) và sản xuất theo nhu cầu (JIT). Chúng ta sẽ khám phá ưu điểm, hạn chế và cách áp dụng chúng, đặc biệt trong bối cảnh sản xuất tại Việt Nam.
I. Khái Niệm Các Phương Pháp Quản Lý Sản Xuất
Trước khi so sánh chi tiết, việc hiểu rõ khái niệm của từng phương pháp quản lý sản xuất là nền tảng để doanh nghiệp áp dụng hiệu quả. Dưới đây là định nghĩa, nguồn gốc và cách hoạt động cơ bản của MRP, Kanban và Just In Time (JIT), được trình bày rõ ràng và thực tiễn, đặc biệt trong bối cảnh sản xuất tại Việt Nam.
1. MRP (Material Requirements Planning) – Lập Kế Hoạch Nhu Cầu Vật Liệu
- Khái niệm: MRP là một phương pháp quản lý sản xuất dựa trên hệ thống phần mềm, giúp lập kế hoạch và quản lý nguyên vật liệu cần thiết cho quá trình sản xuất. Nó tính toán số lượng, thời gian và loại vật tư dựa trên lịch sản xuất tổng thể (Master Production Schedule – MPS) và danh sách vật liệu (Bill of Materials – BOM).
- Nguồn gốc: Được phát triển bởi Joseph Orlicky vào năm 1964 tại IBM, MRP ra đời để giải quyết vấn đề quản lý tồn kho phức tạp trong sản xuất hàng loạt tại Mỹ. Đây là bước tiến từ quản lý thủ công sang tự động hóa bằng máy tính.
- Lợi ích: Giảm chi phí tồn kho, lập kế hoạch chính xác, tối ưu hóa nguồn lực lao động và máy móc.
- Hạn chế: Ít linh hoạt, phụ thuộc vào dữ liệu đầu vào chính xác, và giả định thời gian đặt hàng cố định, dễ gặp rủi ro khi chuỗi cung ứng biến động.
2. Kanban – Hệ Thống Quản Lý Dòng Chảy Theo Nhu Cầu
- Khái niệm: Kanban là một phương pháp quản lý sản xuất thuộc hệ thống tinh gọn (Lean Manufacturing), sử dụng tín hiệu trực quan (thường là thẻ Kanban) để điều phối sản xuất và tồn kho theo nhu cầu thực tế, thay vì dự báo.
- Nguồn gốc: Được phát triển bởi Taiichi Ohno tại Toyota (Nhật Bản) vào những năm 1940-1950, Kanban lấy cảm hứng từ cách siêu thị quản lý hàng hóa – chỉ bổ sung khi kệ trống. Tên “Kanban” trong tiếng Nhật nghĩa là “thẻ tín hiệu” hoặc “bảng hiệu”.
- Lợi ích: Giảm tồn kho, cải thiện dòng sản xuất, tăng tính linh hoạt, đặc biệt trong sản xuất lặp lại.
- Hạn chế: Yêu cầu kỷ luật cao, phức tạp khi triển khai ban đầu, và phụ thuộc vào chuỗi cung ứng ổn định.
3. Just In Time (JIT) – Sản Xuất Đúng Lúc
- Khái niệm: Just In Time (JIT) là một phương pháp quản lý sản xuất nhằm sản xuất và giao hàng đúng số lượng, đúng thời điểm khách hàng cần, loại bỏ hoàn toàn tồn kho không cần thiết và tối ưu hóa hiệu quả.
- Nguồn gốc: Cũng xuất phát từ Toyota (Nhật Bản) trong những năm 1950, JIT là một phần của Hệ Thống Sản Xuất Toyota (Toyota Production System – TPS), được thiết kế để cạnh tranh với các nhà sản xuất phương Tây bằng cách giảm lãng phí và nâng cao chất lượng.
- Lợi ích: Giảm chi phí lưu kho, cải thiện chất lượng sản phẩm, tăng hiệu quả sản xuất.
- Hạn chế: Dễ bị gián đoạn nếu chuỗi cung ứng không ổn định, đòi hỏi đầu tư ban đầu lớn và thay đổi văn hóa doanh nghiệp.
II. So sánh ứng dụng thực tiễn của từng phương pháp
1. MRP (Lập Kế Hoạch Nhu Cầu Vật Liệu)
Cách hoạt động: MRP hoạt động theo nguyên tắc “đẩy” (push system), nghĩa là sản xuất dựa trên dự báo nhu cầu. Dữ liệu đầu vào (MPS, BOM, tồn kho) được xử lý để tạo ra kế hoạch đặt hàng hoặc sản xuất bổ sung.
Thực tiễn tại Việt Nam: MRP phổ biến trong các ngành cần lập kế hoạch dài hạn như cơ khí, điện tử, nơi sản phẩm có nhiều linh kiện phức tạp. Tuy nhiên, nó yêu cầu dữ liệu chính xác và chuỗi cung ứng ổn định – thách thức lớn khi logistics Việt Nam thường biến động.
2. Kanban (Hệ Thống Kéo)
Cách hoạt động: Kanban hoạt động theo nguyên tắc “kéo” (pull system), sản xuất chỉ bắt đầu khi có tín hiệu từ bước tiếp theo trong dây chuyền. Khi một công đoạn hoàn thành và cần nguyên liệu, thẻ Kanban được gửi ngược lại để yêu cầu bổ sung.
Thực tiễn tại Việt Nam: Kanban phù hợp với các ngành sản xuất lặp lại như dệt may, lắp ráp điện tử, nơi nhu cầu thay đổi nhanh và cần giảm lãng phí. Tuy nhiên, nó đòi hỏi kỷ luật cao từ nhân viên và nhà cung cấp.
3. Just In Time (JIT) (Sản Xuất Đúng Lúc)
Cách hoạt động: JIT hoạt động theo nguyên tắc “kéo” (pull system), sản xuất chỉ diễn ra khi có đơn hàng cụ thể, không dự trữ nguyên liệu hay thành phẩm. Nó yêu cầu sự đồng bộ hoàn hảo giữa các khâu sản xuất và chuỗi cung ứng.
Thực tiễn tại Việt Nam: JIT hiệu quả trong các ngành có chuỗi cung ứng ổn định như ô tô, điện tử cao cấp, nhưng dễ bị gián đoạn tại Việt Nam do tắc nghẽn logistics hoặc thời tiết (mưa lũ). Một số doanh nghiệp kết hợp JIT với dự trữ tối thiểu để giảm rủi ro.
IV. Chi phí Triển Khai và ROI Của Các Phương Pháp Quản Lý Sản Xuất
Chi phí triển khai và lợi tức đầu tư (ROI) là yếu tố quan trọng khi chọn phương pháp quản lý sản xuất:
- MRP: Chi phí ban đầu cao (phần mềm, đào tạo, nhập liệu), khoảng 50-100 triệu VNĐ cho doanh nghiệp vừa, nhưng ROI đạt 150-200% sau 12-18 tháng nhờ giảm tồn kho và tối ưu nguồn lực.
- Kanban: Chi phí thấp (chủ yếu là thẻ tín hiệu hoặc phần mềm đơn giản), khoảng 10-20 triệu VNĐ, ROI nhanh (100-150% trong 6-12 tháng) nếu chuỗi cung ứng ổn định.
- JIT: Chi phí trung bình (đào tạo, cải tiến quy trình), khoảng 30-70 triệu VNĐ, ROI cao (200-300% trong 18-24 tháng) nhưng rủi ro lớn nếu chuỗi cung ứng không đồng bộ.
V. Xu hướng và ứng dụng tại Việt Nam năm 2025
Năm 2025, công nghệ như AI và IoT đang thay đổi cách áp dụng các phương pháp quản lý sản xuất. AI cải thiện dự báo nhu cầu trong MRP, trong khi IoT hỗ trợ Kanban và JIT bằng dữ liệu thời gian thực. Một chi tiết thú vị là nhiều doanh nghiệp Việt Nam, như ngành dệt may ở Đồng Nai, đang kết hợp MRP với Kanban để vừa lập kế hoạch dài hạn vừa điều chỉnh ngắn hạn, tăng 25% hiệu suất, theo báo cáo từ một hội thảo công nghệ sản xuất.
Xu Hướng Kết Hợp Các Phương Pháp Quản Lý Sản Xuất Trong Tương Lai
Năm 2025, xu hướng “Hybrid Approach” (kết hợp lai) đang nổi lên:
- MRP + Kanban: MRP lập kế hoạch dài hạn, Kanban điều chỉnh ngắn hạn. Một nhà máy điện tử ở TP.HCM dùng cách này, tăng 25% hiệu suất dây chuyền.
- JIT + MRP: MRP dự báo nhu cầu, JIT tối ưu giao hàng. Một công ty ô tô ở Hải Phòng giảm 20% chi phí logistics nhờ kết hợp.
- Kanban + JIT: Kanban quản lý dòng chảy, JIT đảm bảo không tồn kho. Một nhà máy may mặc ở Đồng Nai tăng 30% tốc độ giao hàng.
Việc chọn phương pháp quản lý sản xuất phụ thuộc vào:
- Loại sản phẩm: Sản phẩm phức tạp chọn MRP, sản xuất lặp lại chọn Kanban, sản lượng cao chọn JIT.
- Tính ổn định của nhu cầu: Nhu cầu biến động chọn Kanban, nhu cầu ổn định chọn MRP hoặc JIT.
- Chuỗi cung ứng: Nếu chuỗi cung ứng không ổn định, tránh JIT, ưu tiên MRP hoặc Kanban.
VII. Đo Lường Hiệu Quả Thực Tế Của Các Phương Pháp Quản Lý Sản Xuất
Để đánh giá phương pháp quản lý sản xuất có hiệu quả, doanh nghiệp cần theo dõi các chỉ số sau:
- Tỷ lệ sử dụng năng lực (Capacity Utilization Rate): MRP tối ưu hóa máy móc tốt hơn (80-90%), trong khi JIT và Kanban phụ thuộc nhu cầu (70-85%).
- Thời gian chu kỳ sản xuất (Production Cycle Time): JIT giảm thời gian nhanh nhất (giảm 30-40%), Kanban trung bình (20-25%), MRP chậm hơn (10-15%).
- Tỷ lệ lỗi sản phẩm (Defect Rate): JIT cải thiện chất lượng tốt nhất (giảm 20%), Kanban ổn định (10-15%), MRP ít ảnh hưởng trực tiếp.
Công thức đơn giản:
- Tỷ lệ sử dụng năng lực = (Thời gian máy móc hoạt động / Tổng thời gian khả dụng) × 100
- Thời gian chu kỳ sản xuất = Tổng thời gian từ nguyên liệu đến sản phẩm hoàn thiện
- Theo dõi các chỉ số này hàng tháng để điều chỉnh phương pháp. Ví dụ, nếu tỷ lệ lỗi cao, kết hợp JIT với kiểm soát chất lượng chặt chẽ hơn.
VIII. Rủi Ro Thực Tế Và Cách Phòng Ngừa Khi Áp Dụng Phương Pháp Quản Lý Sản Xuất
Mỗi phương pháp đều có rủi ro riêng tại Việt Nam, nơi logistics và lao động biến động:
- MRP: Sai dữ liệu đầu vào (như tồn kho không chính xác) dẫn đến đặt hàng thừa/thiếu. Giải pháp: Dùng phần mềm kiểm tra dữ liệu tự động và kiểm kê định kỳ.
- Kanban: Nhu cầu đột biến làm quá tải hệ thống thẻ tín hiệu. Giải pháp: Dự trữ “buffer stock” nhỏ (5-10% nhu cầu) cho các sản phẩm chủ lực.
- JIT: Gián đoạn chuỗi cung ứng (như tắc nghẽn cảng) làm ngừng sản xuất. Giải pháp: Xây dựng mạng lưới nhà cung cấp phụ (backup suppliers) trong nước.
IX. Giới Thiệu Giải Pháp MES SmartTrack của Vietsoft – Đột Phá Trong Quản Lý Sản Xuất
Sau khi khám phá các phương pháp quản lý sản xuất như MRP, Kanban và Just In Time, bạn có thể tự hỏi: Làm sao để triển khai chúng hiệu quả hơn trong thực tế, đặc biệt tại Việt Nam? Đây là lúc MES SmartTrack từ Vietsoft – một giải pháp giám sát sản xuất thông minh – trở thành “người bạn đồng hành” lý tưởng cho doanh nghiệp của bạn.
1. MES SmartTrack Là Gì Và Lợi Ích Ra Sao?
MES SmartTrack là hệ thống quản lý sản xuất (Manufacturing Execution System) được phát triển bởi Vietsoft, tích hợp công nghệ hiện đại để giám sát và tối ưu hóa dây chuyền sản xuất theo thời gian thực. Nó không chỉ hỗ trợ các phương pháp như MRP, Kanban hay JIT mà còn nâng tầm hiệu quả vượt xa mong đợi:
- Hỗ trợ MRP: Tự động hóa nhập liệu cho BOM và MPS, giảm sai sót và tăng tốc lập kế hoạch nguyên vật liệu lên đến 30%.
- Tăng cường Kanban: Thay thế thẻ tín hiệu thủ công bằng giám sát số hóa, giúp quản lý dòng chảy sản xuất chính xác hơn, giảm 20% thời gian chờ.
- Hoàn thiện JIT: Theo dõi trạng thái nguyên liệu và giao hàng tức thì, đảm bảo sản xuất đúng lúc mà không lo gián đoạn chuỗi cung ứng.
MES SmartTrack không chỉ là công cụ, mà còn là chìa khóa để tối ưu hóa bất kỳ phương pháp quản lý sản xuất nào bạn chọn. Xin vui lòng tham khảo giải pháp Hệ thống giám sát sản xuất MES SmartTrack tại đây
Hoặc liên hệ để nhận tư vấn theo hotline: 0986778578 hoặc email sales@vietsoft.com.vn
X. Kết luận
Mỗi phương pháp quản lý sản xuất – MRP, Kanban, JIT – đều có giá trị riêng, phù hợp với các tình huống khác nhau. Doanh nghiệp Việt Nam có thể kết hợp chúng để tối ưu hóa, đặc biệt với sự hỗ trợ từ công nghệ hiện đại. Hãy đánh giá kỹ nhu cầu và nguồn lực để chọn phương pháp phù hợp nhất.